The production of glass—one of humanity’s oldest materials—is getting a 21st century makeover. A new approach to glassmaking treats the material like plastic, allowing scientists to injection mold vaccine vials, sinuous channels for carrying out lab chemistry, and other complex shapes.
“It’s a really exciting paper,” says André Studart, a materials scientist at ETH Zürich. “This is a great way to form glass into complicated and interesting geometries.”
[…]
In 2017, researchers led by Frederik Kotz, a microsystems engineer at the Albert Ludwig University of Freiburg, set out to change that. They reworked a 3D printer to forge glass rather than printing plastics or metals.
The scientists created a printable powder by mixing silica nanoparticles with a polymer that could be cured with ultraviolet (UV) light. After printing the shapes they wanted, they cured the polymer with UV light so it would hold its shape. They then fired the mix in an oven to burn off the polymer and fuse the silica particles into a continuous glass structure.
The approach worked, making it possible to craft shapes such as tiny pretzels and replica castle gates. The work garnered interest from companies wanting to build minute lenses and other complex transparent optical components for telecommunications equipment. But the procedure was slow, turning out components one by one, rather than a fully industrial approach that could produce parts en masse, as is done with plastic.
To speed things up, Kotz and his colleagues have now extended their nanocomposite approach to work with injection molding, a process used to mass produce plastic parts like toys and car bumpers by the ton. The researchers again started with tiny silica particles. The team then mixed the silica with two polymers, polyethylene glycol (PEG) and polyvinyl butyral (PVB). The mixture created a dry powder with the consistency of toothpaste. The team fed the paste into an extruder that pressed it into a preformed mold with shapes such as a disc or tiny gear.
Outside of the mold, the parts hold their shape because myriad weak attractive bonds, called van der Waals interactions, form between neighboring silica particles. But the parts are still fragile.
To harden them, the researchers used water to wash away the PEG. They then fired the remaining material in two stages: First at 600°C to burn out the PVB, and second at 1300°C to fuse the silica particles into the final piece.
“What you get in the end is high purity silica glass” in any shape you want, Kotz says. The glass parts also end up with the optical and chemical characteristics needed for commercial telecommunications devices and chemical reactors, he and his colleagues report today in Science.
[…]
However, Studart says this new approach to mass producing glass parts still faces a bottleneck: Washing away the PEG must be done slowly, over days, to ensure the glass parts don’t crack. Speed that up, he says, and injection molding of glass could become as popular as it is with plastic.
Source: Glass molded like plastic could usher in new era of complex glass shapes | Science | AAAS
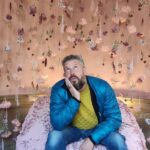
Robin Edgar
Organisational Structures | Technology and Science | Military, IT and Lifestyle consultancy | Social, Broadcast & Cross Media | Flying aircraft